Gas Hazards Within Breweries

Gas Hazards Within Breweries
A brewery refers to the actual building where beer or malt liquors are produced. Many people view beer brewing as an artistic endeavour, but the reality is that there is a rigorous science at work here. Breweries in the current day are held to the same high standards for safety as they are for the quality of their products. There are various gas hazards within breweries that can pose a risk to employees.
There are four main steps in brewing, and during this process, there are many gas hazards that can arise. Let's look at these steps in more detail below.
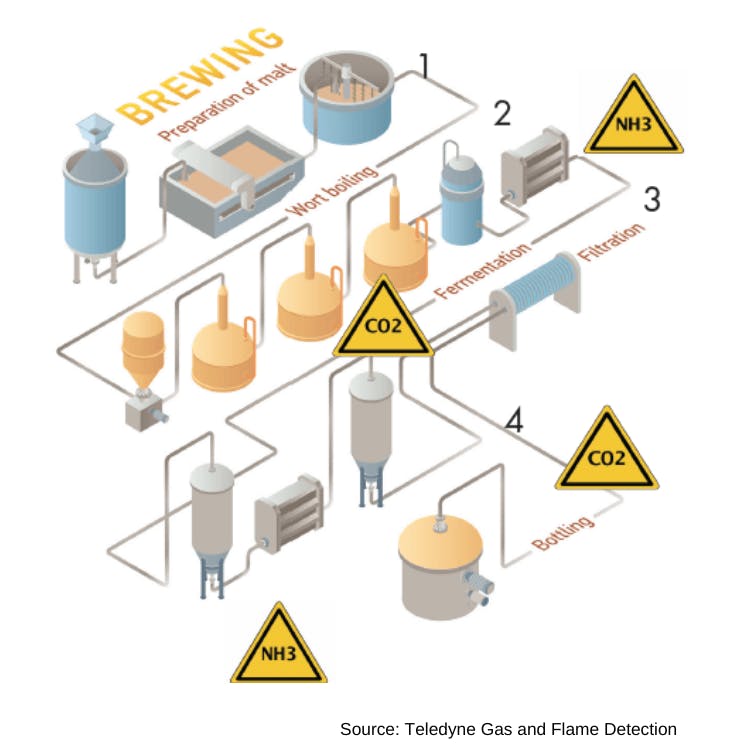
Malting Process
In order to encourage germination, malt is washed and steeped in water during the malting process. Once germination is complete, the malt is rinsed, dried in kilns, and sorted. Prior to the brewing process, malt is crushed and water is added, converting the starch into malt sugar. The Lautering process is then initiated, removing the draff to leave only the liquid wort.
Preparing the Wort
After collecting the liquid wort, it is heated in the brewing kettle and hops are added. The extract is subsequently extracted from the wort using whirling.
Fermenting Process
After cooling the wort, yeast is added during the fermentation phase. The method consists of two major phases: primary fermentation and secondary fermentation, which occur in two distinct tanks so that the beer can rest and mature appropriately. Carbon Dioxide (CO2) is a byproduct of the fermentation process; dangerously excessive concentrations can be fatal.
Packaging and Distribution
For distribution, beer might be filled into bottles, barrels, or cans. Before packaging, certain beers undergo filtration, while others are packed in their natural, unfiltered state. Leaks of ammonia from the beer's refrigeration system can be harmful.
What are the risks within breweries?
Ammonia (NH3) can pose a threat at low levels, causing irritation to the eyes, lungs, and skin. Higher levels of NH3 can cause severe lung damage and possibly blindness. During the refrigeration of beer, ammonia can be a risk.
Methane (CH4) is a danger to brewery employees in boiler rooms. Methane is a combustible gas and can be a risk of ignition, particularly in confined spaces.
Carbon Dioxide (CO2) is also dangerous to employees as it can be produced during fermentation. It can cause shortness of breath and headaches with a ppm range of between 30,000 ppm and 75,000 ppm. Anything over these levels can end up being fatal. In addition to the dangers in breweries, CO2 is also used to dispense beer.
Nitrogen (N2), while present in the air along with CO2, can also be hazardous to employees. N2 is not a toxic gas; however, it can displace oxygen. This can cause asphyxiation due to a lack of breathable air.
What safety measures should be in place?
Developing solutions for working in breweries requires acknowledging and understanding the dangers. Workers participating in each phase of the brewing process should be equipped with specialised protection to do their daily tasks safely. As much manual labour and maintenance are needed, it is doubtful that the dangers will be eliminated. Therefore, gas detection and protection models must be in place to provide the best safety to employees.

Working in a confined space in breweries
Confined spaces are among the most dangerous areas in breweries. The regions and processes where carbon dioxide might be present in a brewery are the beer storage tanks, pumping stations, bottling areas, silos, and the carbonation process itself. Carbon dioxide gas can accumulate in confined places such as fermentation tanks, kegs, mixing tanks, and silos as a byproduct of the brewing process.
Workers must be equipped with personal gas detection to complete pre-entry tests and protect their safety while in tight places. Using a pumped gas detector to perform clearance checks allows for possibly hazardous gas to be monitored before an employee enters the space. Once this inspection has been completed and determined that it is safe to enter, continual personal monitoring must be conducted. Due to factors such as leakage, the concentration of gases in a confined space can fluctuate rapidly; continual monitoring is essential.
Products for Detection
Our recommended multi-gas detectors some of which can be used in breweries for confined space pre-entry, personal protection, or area monitoring.
Products for Protection
Our recommended personal protection equipment for conduction pre entry checks, maintenance or hazard escape in breweries.